Textile market
Consumers in fast-growing developing economies are increasingly able to purchase fabrics with design appeal and designer clothing with a rising standard of living and a significant increase in GDP per capita. At the same time, the public's increasing interest in artistic fabrics is also conducive to the growth of the entire textile market. Rising purchasing power, relatively stable population growth and rapidly changing fashion trends in today's society are decisive factors driving the growth of the textile market.
Printing technology for Textiles
The fashion of fabrics is closely related to the improvement of fabric printing technology. There are many printing technologies on the market today, screen printing and inkjet printing are the most commonly used for textiles.
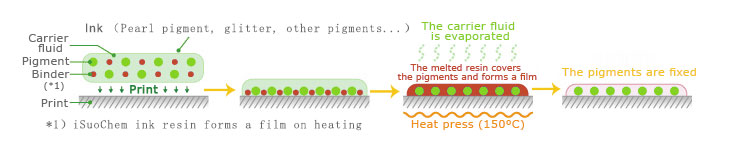
Textile printing technology is based on various resins as a carrier, composed of pigments or dyes and related additives, and has good adhesion. Through printing, text and pictures are printed on fabrics.
Printing ink or color paste for textiles
Before printing the fabric, you must first choose a good printing ink or color paste. The quality of printing ink and color paste determines the effect of textile printing. To manufacture of a good textile printing ink or color paste, the choice of raw materials, especially the choice of pigments used in the ink, is particularly important.
Pigment for textile printing
Currently, the following are very specific and market-leading pigments for textiles printing:
1. Pearlescent pigment for textiles: Has a silky pearl effect
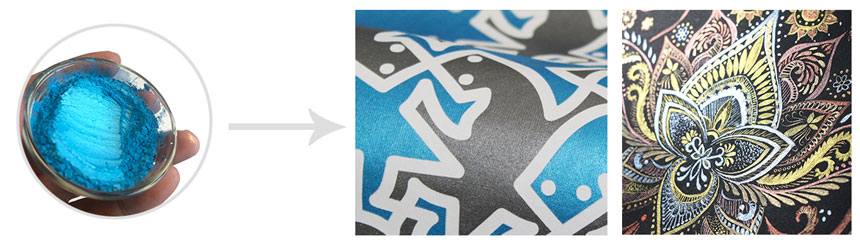
2. Glitter powder for textiles: Make the fabric sparkle, it is the darling of children and the fashion industry.
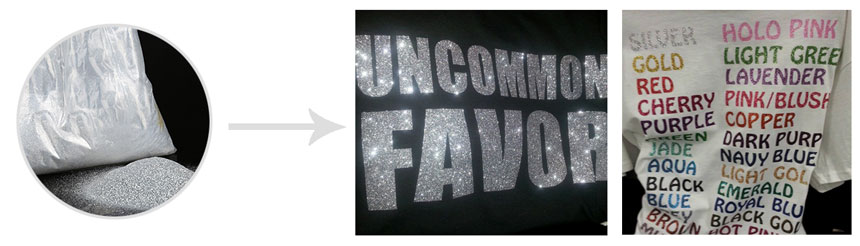
3. Glowing in the dark pigment for textiles: It can glow by itself at night.
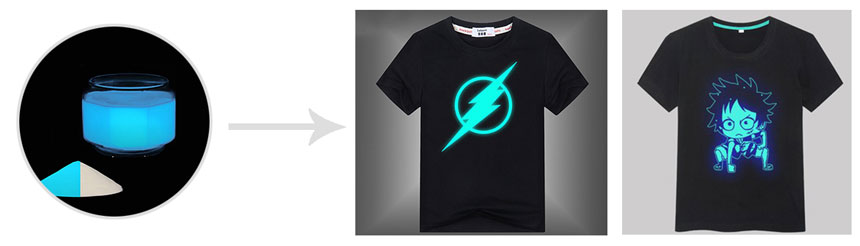
4. Photochromic pigment for textiles: It is a new product developed by micro-encapsulation technology, and will show color under sunlight or UV light and hide the color after leaving sunlight or UV light.
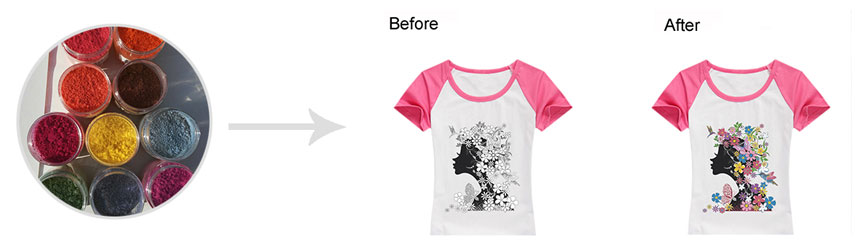
5. Thermochromic pigment: It adopts temperature sensitive microcapsules and color change by temperature rising or falling in a certain range.
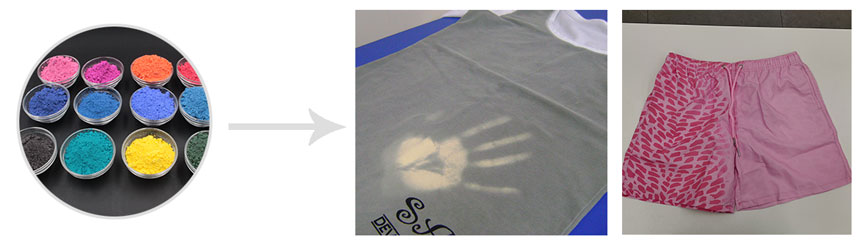
6. Fluorescent pigment for textiles: This is a kind of organic pigment that can emit fluorescence after light excitation. The light source used for excitation can be ultraviolet light or sunlight. This pigment glows and does not last in the dark.
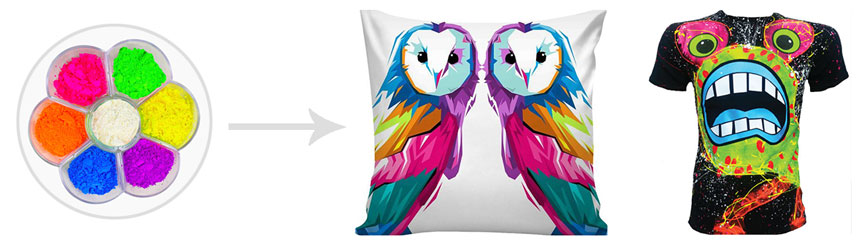
7. Bronze powder for textiles: Compared with Pearlescent pigment, it has stronger metallic feeling.
8. Reflective pigment for textiles: This product can be directly added to paint or resin, so that the product has a retro-reflective effect, and can be used on surfaces of various complex shapes. It is the core raw material for the production of reflective fabrics, reflective films, reflective coatings, reflective signs, advertising materials, apparel materials, standard track, shoes and hats, school bags, water, land and air life-saving supplies and other new light-functional composite materials.
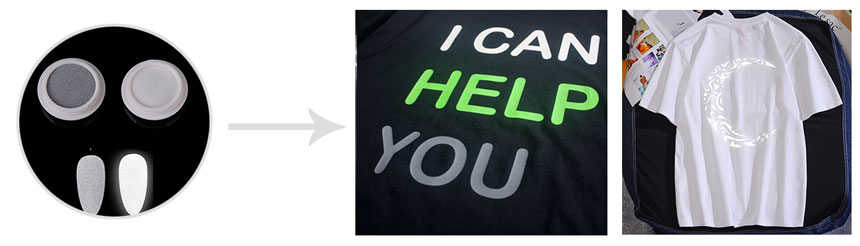
9. Water reactive dye for textiles: After printing this product, the printing areas will show white color on the surface when it's dry. When the surface is wet, the printed area becomes transparent, and the background color shows up.
Tips 1 for screen printing:
For screen printing, the screen mesh determines the average particle size of the pigment used. All pigments are suitable for screen printing, it should be noted that large particle size pigments must be matched with thicker screen.
Tips 2 for making printing ink:
For making printing ink, pigments should be added at the very end of mixing, when all other components have been mixed well. This avoids damage to the pigment due to excessive shearing. During production, firstly to fully wet the pigment with a small amount of solvent, then add a small amount of carrier ink (solution) and stir evenly. Finally, this pre-dispersed ink is added to the remaining transparent ink for further stirring and dispersion. Agitation should be carried out by means of an agitator rotating at high speed with low shear. It takes about 15 minutes to ensure an even dispersion. To prevent damage to the pigment flakes, use of high shear agitation devices such as ball mills, stone mills and three-rollers should be avoided.